Highlights
- Researchers from Citrine Informatics and SLAC National Accelerator Laboratory collaborated to build a closed-loop, autonomous system for design and synthesis of nanoparticles for catalysis.
- Starting with no historical data the system was able to reach multiple objectives in just 12 hours.
- This methodology coupling computer-controlled reactors and machine learning can be rapidly used to understand the process parameters needed to reliably produce nanoparticles of target size and shape in new alloy systems.
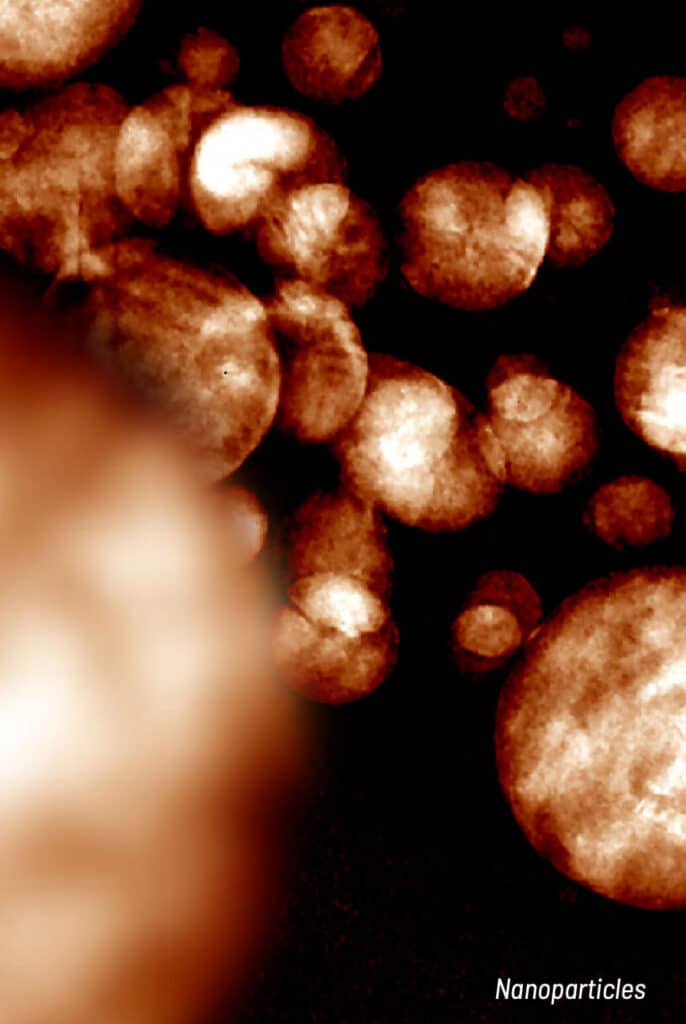
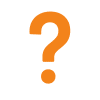
The Motivation
Design and synthesis of new materials is complex, time-consuming and resource intensive, but vital for progress. Being able to tightly couple design and synthesis in an iterative learning loop, without the need for human intervention, reduces costs and enables businesses to explore a broader design space than they perhaps would have, leading in some cases to more differentiated products.
In catalysis, the size, shape, faceting, and chemistry of particles all influence the specificity and the effectiveness of the catalyst. This project focused on being able to reliably produce particles of target size and shape distribution.
The Challenge
Traditional Method
Partnering with researchers at Stanford Synchrotron Radiation Lightsource, SLAC National Accelerator Laboratory1, the Citrine team worked on a project centered on synthesizing colloidal platinum nanoparticles, for catalysis. Particle size and homogeneity need to be tightly controlled in this application. In nanoparticle synthesis, there is no known unified framework for relating the physio-chemical properties of the reagents to the structure of the product, even though these materials have been studied heavily for decades. The aim of the project was to find a high yield method to synthesize nanoparticles with tightly controlled morphologies in a time- and resource-efficient way.
1 J. Chem. Phys. 154, 224201 (2021) – https://aip.scitation.org/doi/full/10.1063/5.0047385
Closed Loop Autonomous Method
The nanoparticles were synthesized in a continuous flow reactor. Computer-controlled pumps were used to pump precise, specified amounts of different chemicals from reservoirs into a heated furnace where the particles nucleate and grow. The temperature of the furnace and flow rate were also computer-controlled. As the particles leave the reactor, they are measured by an in situ smallangle x-ray scattering (SAXS) device. The scattering data is then analyzed to estimate statistics around particle size and distribution of sizes, morphology, and scattering intensity (a proxy for product yield).
The final part of the loop is a machine learning (ML) model that takes input data (chemical quantities, furnace temperature, etc.) and predicts output parameters (particle size, etc.) This ML model is used to select the input parameters for the next experiment based on optimizing the output properties or exploring areas in the design space with high uncertainty. Each time an experiment is run, the data from the experiment is used to retrain the model and improve its accuracy in the region of the target. This, in turn increases the likelihood that the next experiment selected will have improved output properties nearer to the goal.
Limitations
The time a particle stays in a continuous flow reactor cannot be controlled, as it can in traditional batch chemistry. This produces a distribution of residence times resulting in a distribution of nanoparticle growth durations. However, the efficiency of the continuous process had significant advantages in terms of the time needed to run an experiment, which means that a larger design space can be explored.
The Results
The closed loop system performed over 50 unique syntheses in 24 hours without interruption. The first project with this system was to produce an achievable particle size in a known material system. In this way the ability of the closed loop system to autonomously find the synthesis parameters to hit a target particle size could be validated.
Success Criteria
- Minimize Particle Size Variation
- A more homogeneous particle size distribution has a smaller sigma.
- Hit target radius size
- Optimize cost to surface area and hit radius needed for a particular reaction.
- Sufficient product yield
- Efficient use of precursors. This is measured by scattering intensity.
Initial Training Grid
The first 16 experiments followed a grid chosen to reflect expected minimum and maximum synthesis conditions. Their results were then used as training data in the machine learning model. Subsequent experiments were based on the ML model’s predictions.
A recipe meeting all specified constraints was formulated 21 recipes after the initial grid of experiments was completed. This took approximately 12 hours. Experiments 34-50 weren’t necessary; they were carried out to use up reagents.
Summary
Citrine Informatics provides a SaaS AI software platform to accelerate development in materials and chemicals. Scientists and Engineers are empowered to use the system as a copilot in their research projects, with the platform suggesting experiments to perform that will navigate the quickest route to success.
AI models can be created to predict the properties of a material, and then used understand the composition and processing parameters needed to ensure that a material hits target properties.
On a known materials system, the computer-controlled closed-loop system using Citrine’s ML technology was able to optimize nanoparticle size while maintaining high yield and low polydispersity in 21 recipes (about half a days work for the system).
High-throughput, closed-loop, computer-controlled synthesis experimentation using ML models can very efficiently optimize nanoparticle production for catalysis applications.
This project demonstrates the ability of Citrine’s AI technology to accelerate product development goals as part of a closed-loop materials design and synthesis system, even in situations with no initial data.